Manage multiple warehouse locations
As your business grows, so does the importance of an organised warehouse facility. Our ERP systems provide advanced control enabling multiple warehouse locations, so you can optimise your picking and speed up your overall processing of orders. Make organising item locations a dream, with our ERP solutions
Locations, locations, locations
When it comes to your warehouse, optimising it to ensure that goods are in the most efficient places can do wonders to speed up your picking and packing processes. With our solutions, you can fully optimise your warehouse to make sure booking goods in and order picking is as pain-free as possible. Configure locations of any shape, size or layout and reorganise your warehouse to suit your business. All this helps to streamline your processes, meaning picking and packing items, stock replenishment and other tasks can be carried out by your team
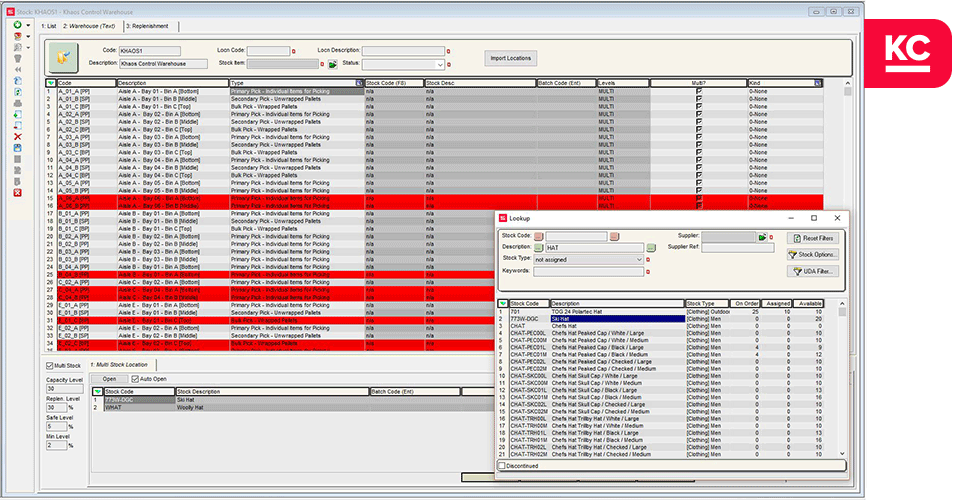
Fully scalable to your needs
As your business grows in size and popularity, your needs are likely to change. Our ERP applications help you manage your growth, and can adjust to fit your changing requirements. Being able to easily manage your warehouse layout means you can adapt your system quickly and easily to fit your physical locations as they change, enabling control, flexibility and support as your business expands
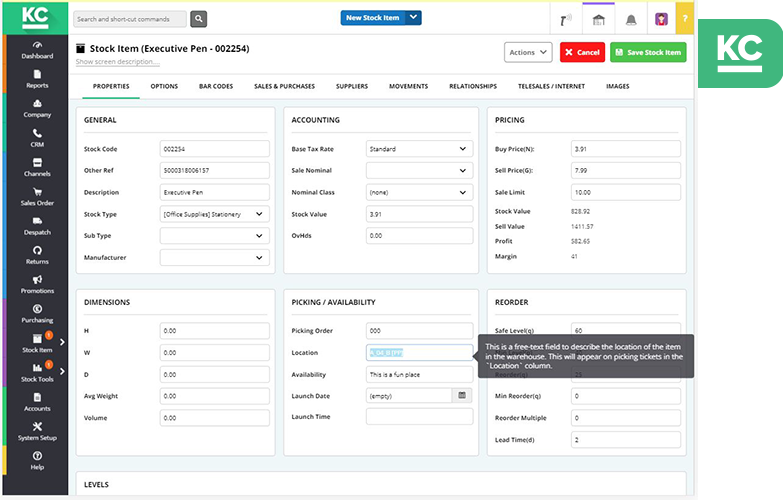
Control your picking faces
Control your picking faces within our solutions by utilising the ability to create different location types in any part of your warehouse. Split up your primary, secondary and bulk locations within the application, and the system will automatically select the appropriate picking and replenishment locations, giving you a detailed overview of your whole warehouse
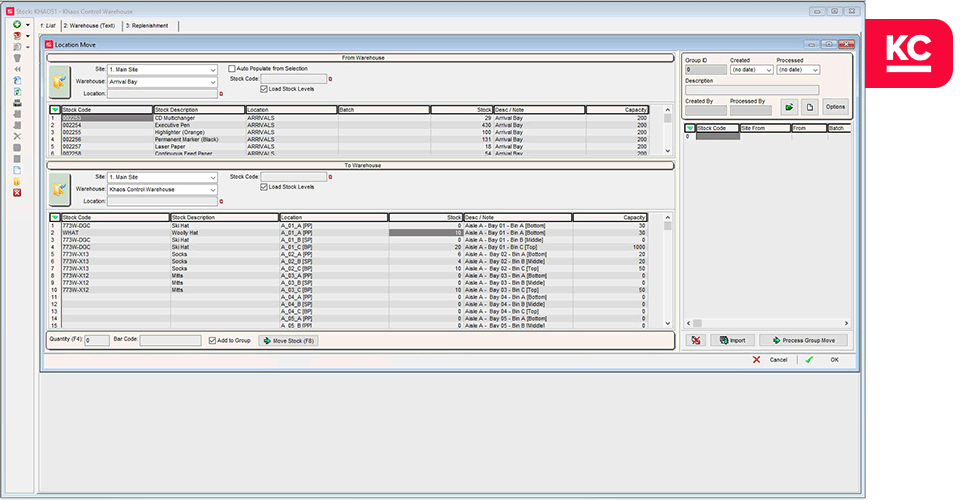
Manage and control your batches with batch control software
Does your stock have expiry dates? Do you need to colour match by batch number? Our batch control software can easily manage your stock batches for you, ensuring different batches are easily identifiable and traceable.
First in, first out goods
Use the batch control software to assign date codes to stock items as they are delivered in and pick from the oldest stock to ensure correct stock rotation.
This feature is a must for businesses that handle perishable or other time-sensitive products, but the scope reaches far beyond that; it can be used as a way of batch colour matching or quality checking.
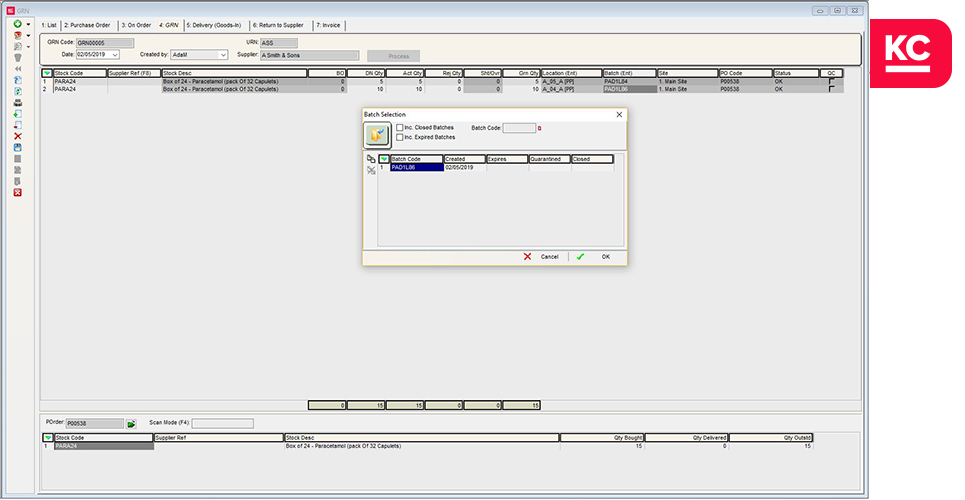
Traceability and control of your stock
Have full traceability of your batch controlled products including batch code labels, allowing for easy recalls or product information updates. Independent stock control by batch, including quarantine, write-off and warehouse locations means you’re always in control. This amount of control allows you to streamline the way your inventory is being run, and really tighten up on the processes you have in place – be that in a stockroom, or a warehouse.
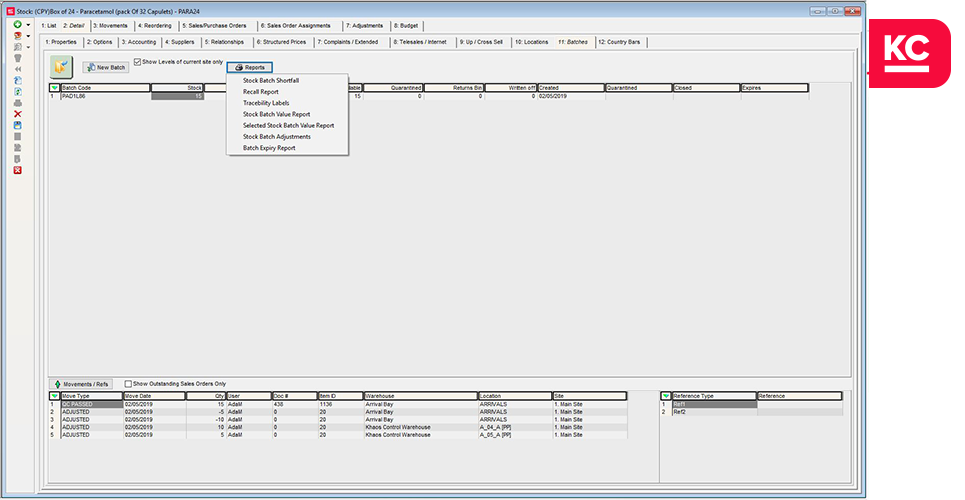
Keep track of your warehouse pallets with
pallet tracking software
Our warehouse pallet tracking software allows you to follow the movements of every pallet in your warehouse. As your business grows, so does the amount of stock in your warehouse, sometimes leading to inaccuracies and time-wasting. Give your warehouse staff the confidence to work efficiently and safely when navigating around the
Control and traceability of your pallets
Pallet codes that follow your stock to its final location mean visibility and traceability of your stock from the moment it enters your warehouse to the point at which it is allocated to your customer sales orders. This level of visibility allows you to work more efficiently when it comes to the turnaround of a customer order, as well picking up on any irregularities within your process.
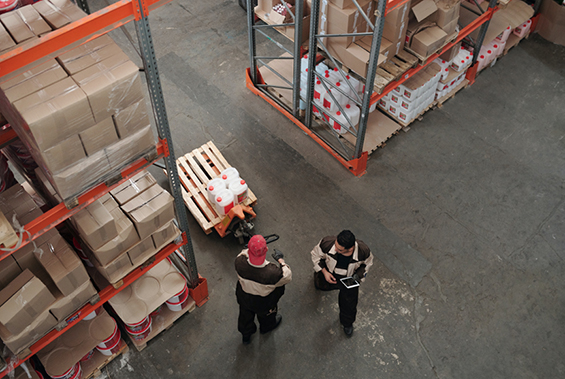
Effective replenishment of your inventory
Make sure that your picking locations are replenished with the right stock at the right time. Whether that’s based on expiry dates or batch matching.
Our pallet tracking software ensures your most sensitive stock is replenished properly, deducing time wasted, as well as any possible returns. This means you can have the confidence that your inventory is running based on reliable information, all for the benefit of your staff (and business!).
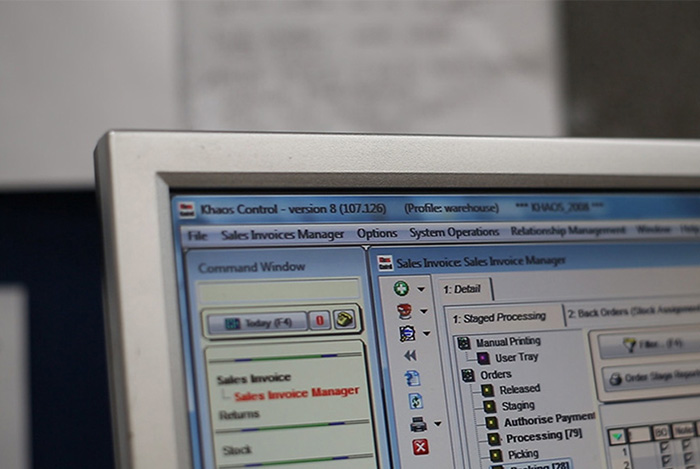
Errors reduced
Booking in bulk stock that shares a batch number or serial number is easily managed using our pallet tracking functionality. For warehouse operatives, that means less time wasted on individually entering different serial numbers, and more time spent moving through orders.
As the processes in your warehouse start to benefit from automating, you’re able to allocate time that require more manual efforts.
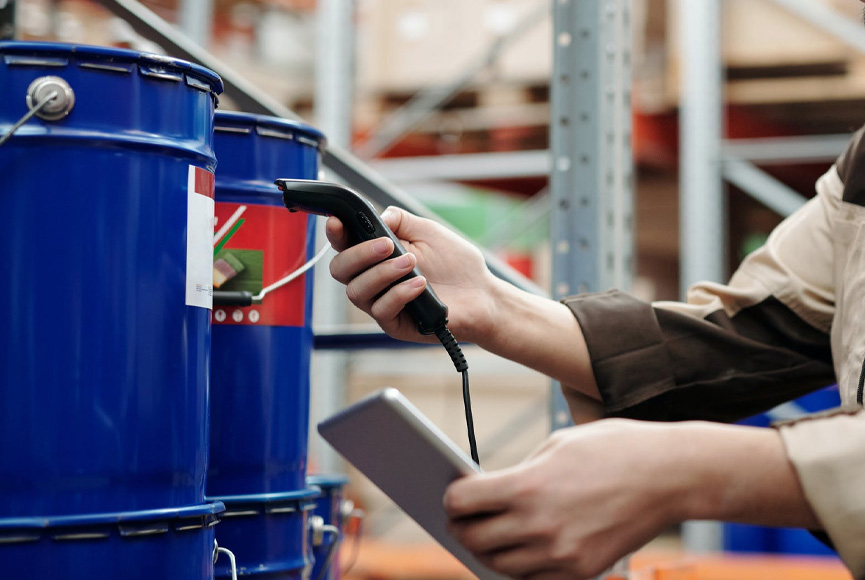
Warehouse allocations
Our warehouse allocations functionality allows you to maximise your warehouse team’s efficiency, as well as gaining complete visibility of who’s doing what, how long it’s taking, and what’s still left to do.
Allocate tasks to the right people
A warehouse allocations system will know what picking, packing or building tasks are waiting and will allocate them to the right team members based on pre-set profiles. By using picking profiles in the system, you’re able to make sure all picks are allocated in a way that no-one is ever overloaded with high volume or excessively heavy orders. The allocation screen will also allow you to to see active and problematic allocations that might need more attention.
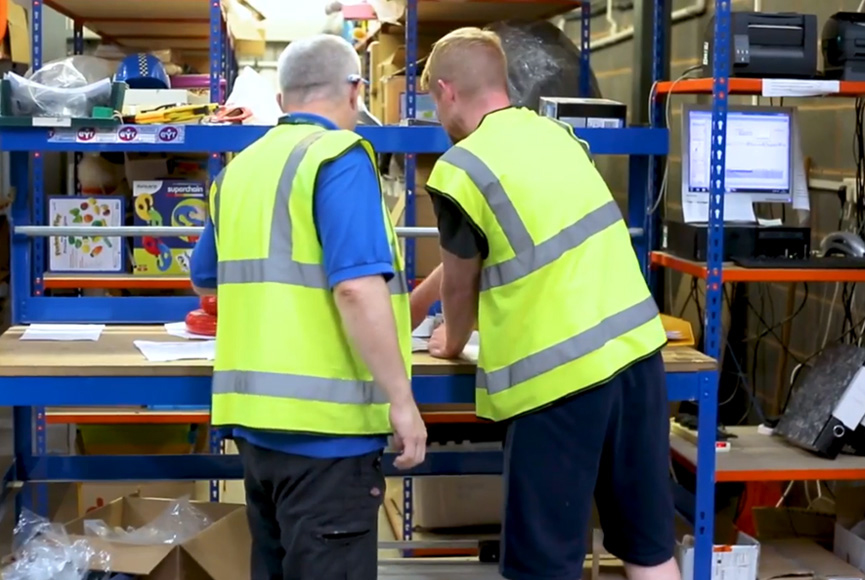
Monitor your team’s performance
Keep an eye on allocation completion rates, error rates and overall stats, whilst allowing your team to easily report problems encountered so that they can be dealt with promptly. Allocation means that everyone knows what they are supposed to be doing, and gives them the tools and the confidence to do it.
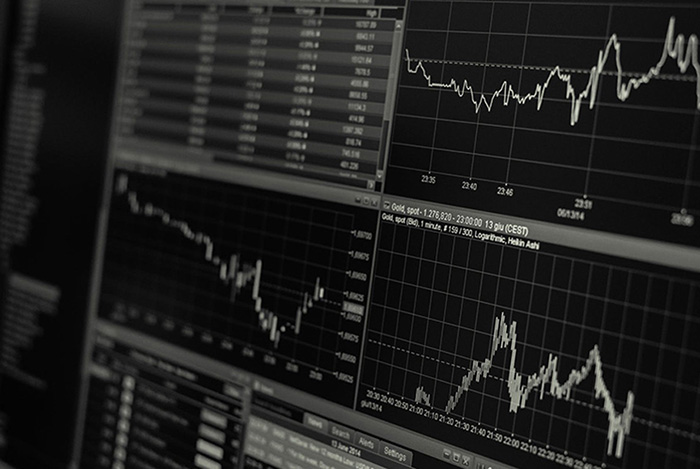
Give your team access to clear and accurate stock information
The ‘in progress’ status that appears over different build tasks also make it clear to warehouse teams who’s working on on what, and what else needs to be done.
More importantly, the system will provide accurate stock levels for those working on more complex builds – ultimately making it easier to work from the ground up.
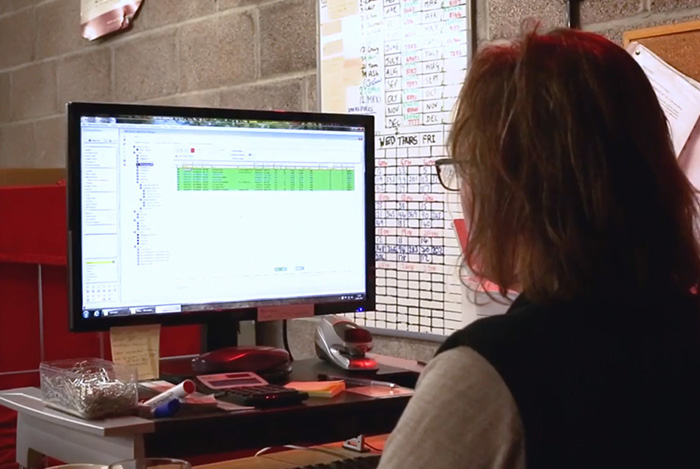